Category

Solenoid Valve Supplier

Home » Application » Solenoid Valve in Air Separation
Solenoid Valve in Air Separation
Solenoid valve is composed of solenoid coil and magnetic core as well as a valve body with one or more holes. When the coil is energized or de-energized, the operation of magnetic core will cause the fluid to pass through the valve body or be cut off, thus changing the direction of fluid. The solenoid part of solenoid valve is composed of fixed iron core, moving iron core, coil and other parts. The valve body is composed of slide spool, slide valve sleeve and spring base. The solenoid coil is directly mounted on the valve body, and the valve body is sealed in the sealing pipe to form a simple and compact combination. Common solenoid valves in production include two-position three-way (3/2) solenoid valve, two-position four-way (4/2) solenoid valve and two-position five-way (5/2) solenoid valve.
3/2-way solenoid valve in oxygen generator
The two-position three-way (3/2) solenoid valve is mostly used in the control system of oxygenerator. The 3/2-way solenoid valve can be used to turn on or cut off the gas supply in production, thus switching the air circuit of pneumatic film head.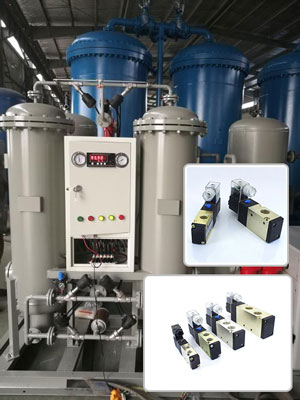
3/2-way pneumatic solenoid valve consists of valve body, valve sleeve, solenoid assembly, spring and sealing structure. The sealing block at the bottom of the moving iron core closes the air inlet of valve body with the help of spring pressure. After powered on, the electromagnet of solenoid valve pulls in and the sealing block with spring on top of moving iron core closes the exhaust port, and then the air flow enters the pneumatic film head from the inlet port to realize the controlling function. When the power is cut off, the electromagnetic force disappears. The moving iron core moves downward from the fixed core under the action of spring force, to open the exhaust port and block the air intake. The air flow of pneumatic film head is discharged through the exhaust port and the diaphragm returns to its original position. In the oxygen generator, the 2-position 3-way pneumatic solenoid valve is used for emergency cut-off at the inlet of turbine expander.
4/2, 5/2-way solenoid valve in air separation
4/2-way solenoid valve and 5/2-way solenoid valve have the same working principle. But the difference is that the former has only one exhaust port, while the latter has two exhaust ports. Two-position four-way solenoid valve is widely used in air separation, and its working principle is as follows.
When the current passes through the coil and excitation is generated, the fixed iron core pulls in the moving iron core, and the moving iron core drives the sliding spool to compress the spring, which changes the position of the spool and thus changes the direction of the fluid. When the solenoid valve coil is out of power, the sliding spool is driven by the elastic force of the spring, and the moving iron core is pushed back to make the fluid flow in the original direction. In oxygen production, the switch of forced valve in the molecular sieve switching system is controlled by a two-position four-way solenoid valve. The air flow is supplied to the piston ends of the forced valve to control the opening and closing of the forced valve.
Solenoid valves are widely used in air separation because of the simple structure and working principle, as well as the convenient installation and use.
3/2-way solenoid valve in oxygen generator
The two-position three-way (3/2) solenoid valve is mostly used in the control system of oxygenerator. The 3/2-way solenoid valve can be used to turn on or cut off the gas supply in production, thus switching the air circuit of pneumatic film head.
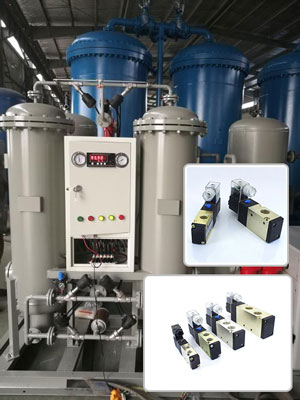
3/2-way pneumatic solenoid valve consists of valve body, valve sleeve, solenoid assembly, spring and sealing structure. The sealing block at the bottom of the moving iron core closes the air inlet of valve body with the help of spring pressure. After powered on, the electromagnet of solenoid valve pulls in and the sealing block with spring on top of moving iron core closes the exhaust port, and then the air flow enters the pneumatic film head from the inlet port to realize the controlling function. When the power is cut off, the electromagnetic force disappears. The moving iron core moves downward from the fixed core under the action of spring force, to open the exhaust port and block the air intake. The air flow of pneumatic film head is discharged through the exhaust port and the diaphragm returns to its original position. In the oxygen generator, the 2-position 3-way pneumatic solenoid valve is used for emergency cut-off at the inlet of turbine expander.
4/2, 5/2-way solenoid valve in air separation
4/2-way solenoid valve and 5/2-way solenoid valve have the same working principle. But the difference is that the former has only one exhaust port, while the latter has two exhaust ports. Two-position four-way solenoid valve is widely used in air separation, and its working principle is as follows.
When the current passes through the coil and excitation is generated, the fixed iron core pulls in the moving iron core, and the moving iron core drives the sliding spool to compress the spring, which changes the position of the spool and thus changes the direction of the fluid. When the solenoid valve coil is out of power, the sliding spool is driven by the elastic force of the spring, and the moving iron core is pushed back to make the fluid flow in the original direction. In oxygen production, the switch of forced valve in the molecular sieve switching system is controlled by a two-position four-way solenoid valve. The air flow is supplied to the piston ends of the forced valve to control the opening and closing of the forced valve.
Solenoid valves are widely used in air separation because of the simple structure and working principle, as well as the convenient installation and use.
Post a Comment:
You may also like: